The Tracked Impact Crusher for Pros
The RM 100GO! tracked impact crusher can compete with much heavier machines in this class. Weighing just 75,000 lbs., it is much easier to break down and move to the next job site. The fuel-efficient diesel-electric drives ensure a low operating cost and less hassle over the machine's lifetime.
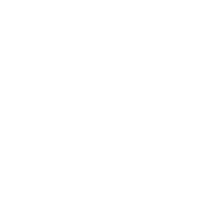
Performance
without sacrificing mobility
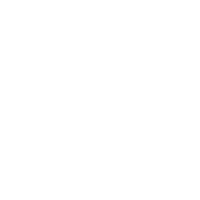
Ease of Use
so anyone can operate it efficiently.
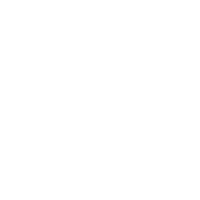
Safety
so you can trust your crew around the machine.
Don't Get Fooled by Its Size— our Tracked Impact Crusher Punches Over Its Weight Class.
Efficiency and productivity are the sum of all components. That's why all components come out of “one mold” to ensure a smooth material flow, so you can minimize downtime and maximize your output.
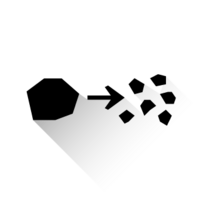
High Reduction Ratio
Adjustable rotor speeds, baffled impact plates, and a proven proprietary impact crusher design for achieving a high throughput capacity.
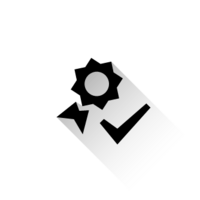
Cuboid Aggregates
Customers Want to Buy
The powerful impact crusher provides multiple settings to adjust your final gradation so you hit spec guaranteed.
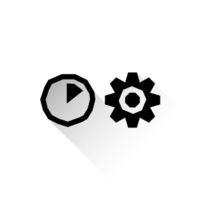
Fast Crusher Adjustment
Our proven single impact wall has three crushing stages, allowing for fast and simple crusher adjustment with only one setting.
Built to Keep You Crushing Longer
We understand that if your crusher is down, your crew is down, and you are bleeding money. Our tracked impact crushers assist you in overfeeding situations or when damages happen so you can resolve issues quickly and put more product on the ground.
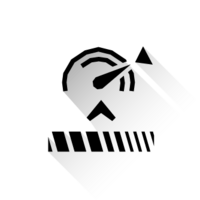
Self-Regulating Feeder
Performance peaks can stall an impact crusher. The self-regulating feeder adjusts the speed, so that you process your material smoothly and keep crushing.
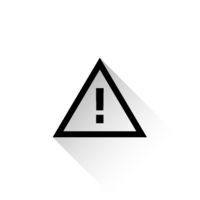
Jam Detection & Overload Protection
Material blockages can result in serious belt damage. RUBBLE MASTER tracked impact crushers shut down the operation automatically to reduce the risk of damages.
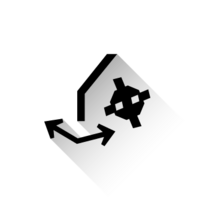
RM Release System
Keep crushing longer by resolving blockages with the touch of a button on your radio remote control.
Operate with the Touch of a Button
The operation of a RUBBLE MASTER compact impact crusher is unlike any other crusher. We focus on making machines less complex so that you can start crushing without the lengthy training necessary because we believe everybody should be able to operate a crusher.
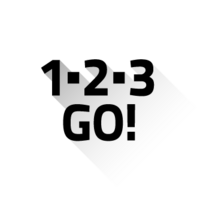
Intuitive and Simple
Less training necessary.
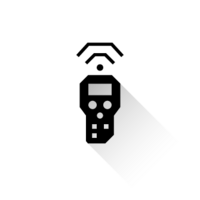
Radio Remote Operated
Run the crusher conveniently & safely from the cab.
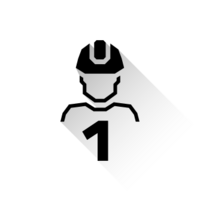
One-Man-Operation
No need for a large crew.
RM XSMART Telemetry Provides More Intelligence About Your Operation
Access machine telemetry and track tonnages conveniently on your cell phone or computer (optional belt scales).
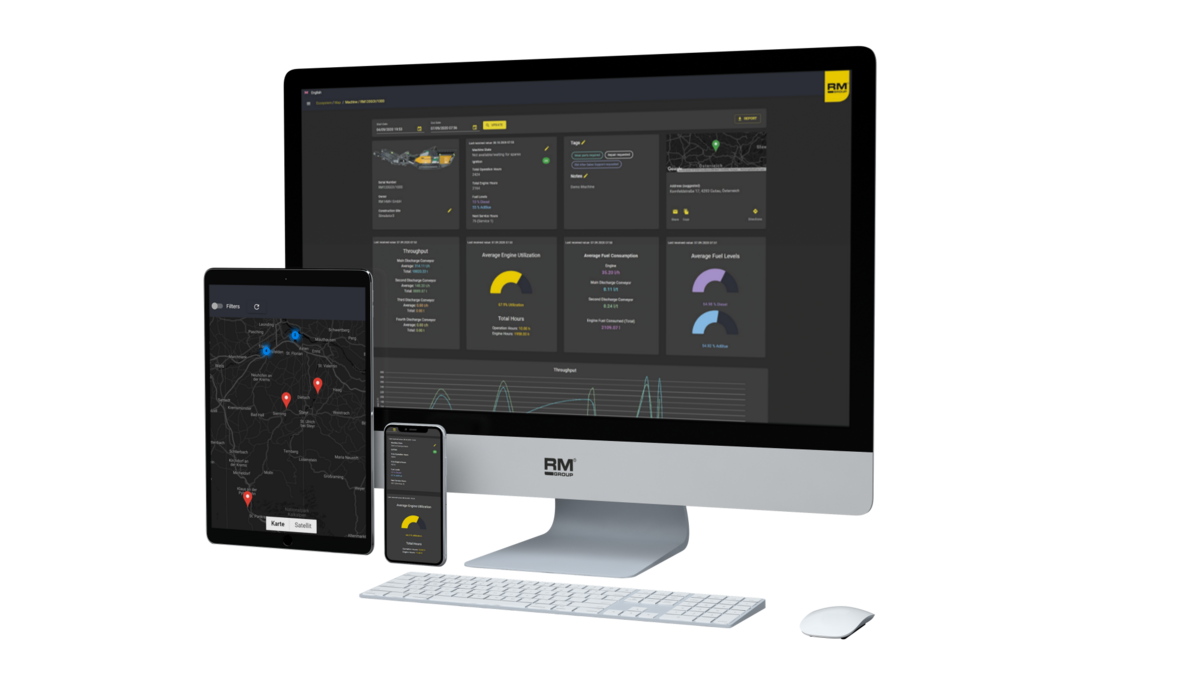
Your safety is important to us.
This is why we keep your feet on the ground.
Climbing ladders with power tools and heavy parts is a safety hazard. All RUBBLE MASTER mobile impactors are fully ground serviceable, which makes light and safe work out of your daily maintenance.
Produce a Cleaner End-Product. Automatically.
The optional wind sifter uses an adjustable air stream to segregate lightweight debris, such as roots and fabrics. Without the wind sifter, you must manually pick contaminants and interrupt your operation more often to clean your screen deck. Improve your bottom line with aggregates people wait in line to buy and less labor involved.
Make more money per produced ton with diesel-electric mobile impact crushers
RUBBLE MASTER has been utilizing diesel-electric drives for its mobile crushers since our beginning in 1991. This well-proven system offers many benefits over conventional diesel-hydraulic drives - most notably its significant lower fuel consumption and surprisingly low noise emissions.
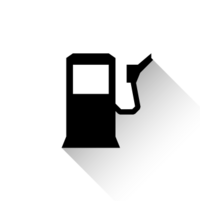
Save Up to 25% on Fuel
compared to traditional diesel-hydraulic tracked impact crushers.
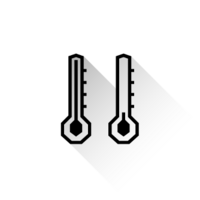
Works Well in Extreme Temperatures
No heating up of hydraulics in winter and no overheating in summer.
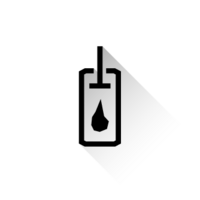
Cut Hydraulic Fluid Costs
Our small hydraulic system is used for auxiliary functions only. Say goodbye to bursting hoses, leaks, and DEP/MOE citations.
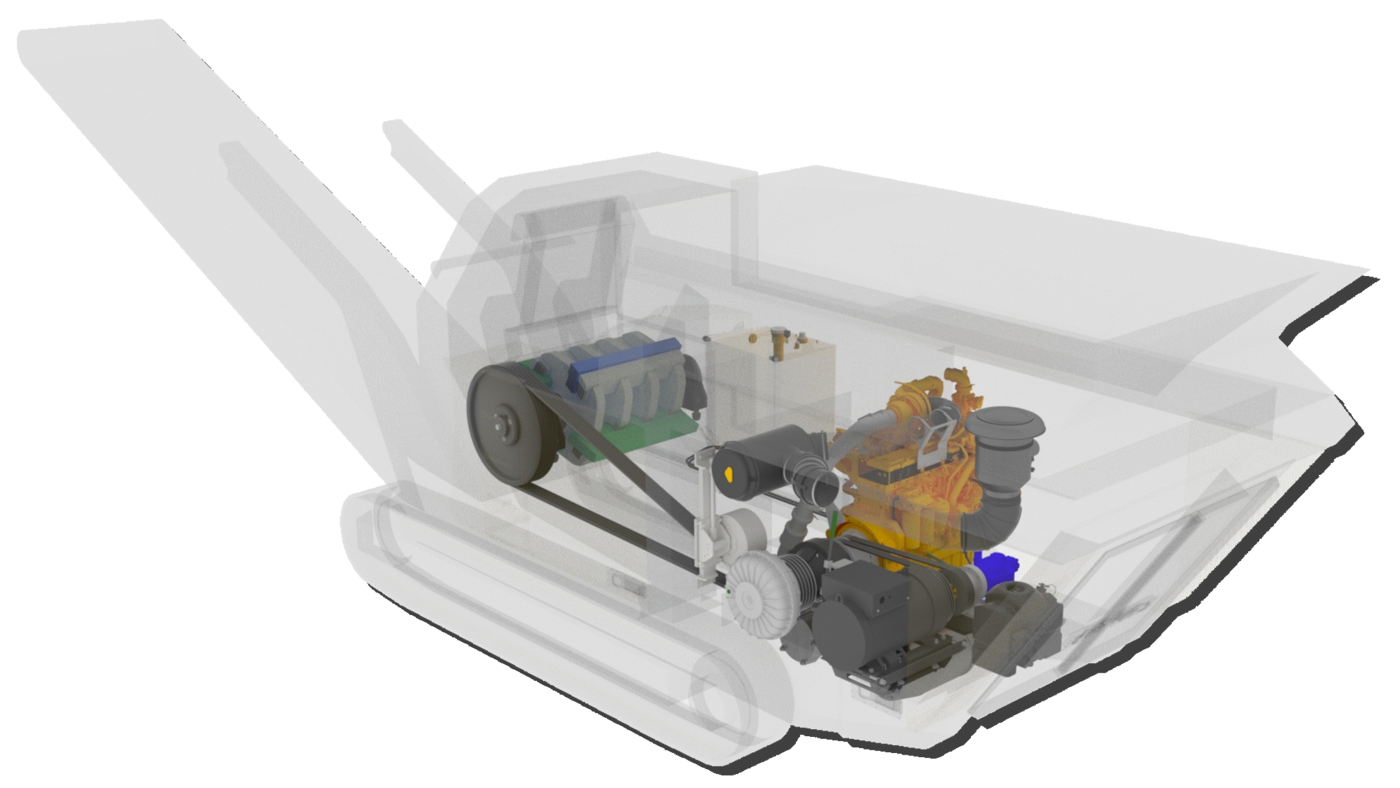
Direct driveX
The diesel engine drives the rotor directly. The RM 100GO! features an optional hybrid drive where an electric motor drives the rotor. This option enables you to operate the crusher from the grid (50Hz grid power needed).
GeneratorX
The generator produces the electric power to run conveyor belts, feeder, and shaker motors.
Small hydraulic pumpX
The small hydraulic system is needed to operate auxiliary functions such as cylinders to setup the machine and adjust the crusher geometry as well as tracking the machine.
Clutch assemblyX
The rotor is engaged/disengaged through a manual clutch. A hydraulic coupling ensures a soft start of the rotor.
Go Anywhere, Anytime
Many crushers in this class require special permits and more than one load to float. The RM 100GO! tracked impact crusher weighs approx 75,000 lbs and is not considered a super-load in many states. This gives you the freedom to mobilize faster and with less preparation time.
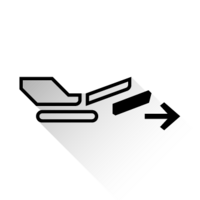
Easy to Detach Screen Attachment
You can break down the machine and move the bare crusher if required. The screen and return conveyor are entirely removed from the crusher.
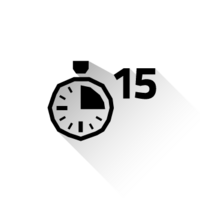
15 Minutes From Trailer to Crushing
A single operator can get the crusher ready without the need of special hand tools.
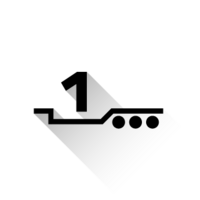
Single move
Unlike other mobile impact crushers in this class, the RM 100GO! can be moved with the screen attached, saving valuable setup and breakdown time.
Perfect for Any Jobsite
Contractors are facing thinner margins due to an increase in smaller jobsites, neighbors’ complaints, and longer trucking times. One versatile RUBBLE MASTER machine can crush any on-site material volume, from just a few hundred tons to very high volumes, virtually putting money back into your pocket.
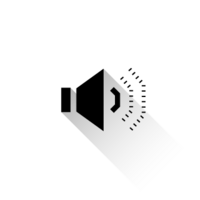
Bar None - The Quietest Crusher
Suprisingly quiet crushing operation.
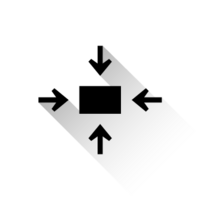
Small Footprint
Ideal for on-site crushing where there is little room for setting up large crushing spreads.
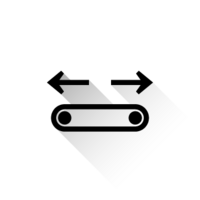
Track & Crush Simultaneously
Eliminates the need for an additional wheel loader or stacking conveyor on-site.
Video Gallery
RM 100GO! Specs
Capacity | up to 250 tph up to 275 TPH |
Inlet opening | 950 x 700 mm 38" x 28" |
Ideal feed size | 560 mm 22 " |
Crusher unit | 4-bar rotor 4-bar rotor |
Feed unit | 3.3 m³ 4.3 yd³ |
Feed height | 3,000 mm 9' 10" |
Prescreen Grizzly (standard) | 1,500 x 900 mm 4'11" x 2'11" |
Screen-box | 1,300 x 3,000 mm 4 x 10 ft |
Drive | diesel-electric diesel-electric |
Transport dimension | 14,700 x 2,860 x 3,155 mm 48'3" x 9'5" x 10'5" |
Weight (no options) | 30,000 kg 66,140 lbs |
Weight incl screen attachment | 34,810 kg 76,742 lbs |
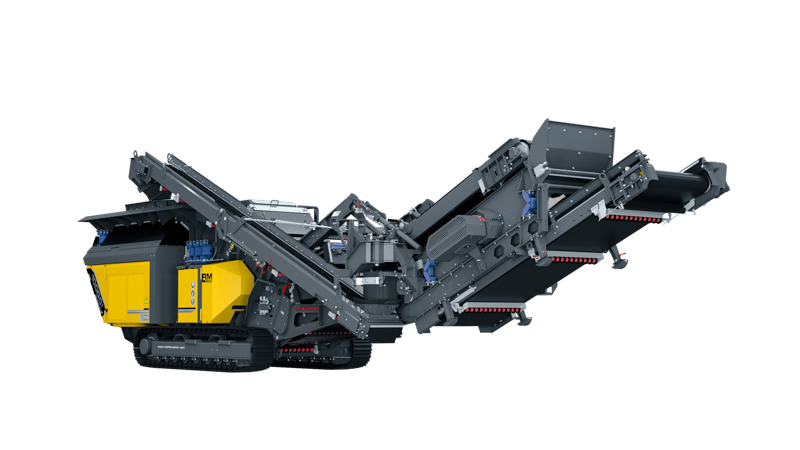
Operating a RUBBLE MASTER
is just…awesome.
Don’t just take our word for it.
"Out of all the crushers we have tried the RUBBLE MASTER puts out the best product around. This machine is putting out product people are waiting in line to buy".
Joe Maggio, Joe Maggio Construction
"The main reason for RUBBLE MASTER is customer service. The second reason that machine does a great job crushing. The third reason my guys understand the machine."
Danny Salomon, Broadway Recycling
Talk to an Expert
Have a question? Fill out the form, and a material processing expert will be in touch with you as soon as possible.