Crushed Basalt
Crushed basalt is used for a wide variety of purposes. It is most commonly crushed for use as an aggregate in construction projects such as road base, concrete aggregate, asphalt stone, railroad ballast, filter stone in drain fields, and may other purposes.
Crushed Basalt
Crushed basalt is used for a wide variety of purposes. It is most commonly crushed for use as an aggregate in construction projects such as road base, concrete aggregate, asphalt stone, railroad ballast, filter stone in drain fields, and may other purposes.
What is basalt rock?
Basalt is an igneous rock that formed from the solidification and cooling of molten rock material (lava or magma). Basalt is typically a dense dark rock colored blue, grey-blue, dark-grey or black with a fine-grained texture. Crushed basalt is used for a wide variety of purposes. It is most commonly crushed for use as an aggregate in construction projects. Crushed basalt is used for road base, concrete aggregate, asphalt pavement aggregate, railroad ballast, filter stone in drain fields, and many other purposes. Basalt is also cut into dimension stone.
Impact Crusher Can be Used as Primary or Secondary Crushers
RUBBLE MASTER mobile impact crushers can process basalt rock as a primary or secondary crusher after a jaw crusher.
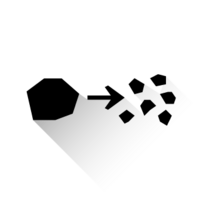
High Reduction Ratio
Ideal for primary and secondary basalt crushing applications.
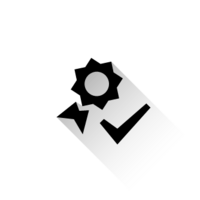
Quality Aggregates
Consistent cubical rock shape. Adjustable aggregate gradation.
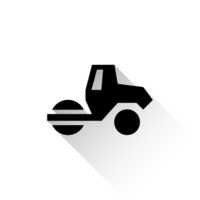
Excellent Compaction
Meet any spec you need with RUBBLE MASTER crushing and screening solutions.
Application Videos
Talk to an Expert
Since 1991, RUBBLE MASTER has brought numerous innovations to the market. We’re crushing & screening experts and work closely with contractors and aggregate producers world-wide.